Zinc Plating
Zinc Plating
Zinc plating, also known as zinc electroplating, is a process in which a layer of zinc is applied to the surface of a metal object to provide corrosion resistance and other desirable properties. It is a widely used method for protecting steel, iron, and other metal substrates from rust and corrosion.
The zinc plating process involves immersing the metal object, known as the substrate or workpiece, into an electrolyte solution containing zinc salts. The workpiece acts as the cathode, while a sacrificial zinc anode is also present in the solution. When an electric current is applied, zinc ions are reduced at the surface of the workpiece, forming a layer of metallic zinc.
The benefits of zinc plating include:
Corrosion protection: The zinc coating acts as a barrier, providing excellent corrosion resistance to the underlying metal substrate. It prevents the substrate from coming into direct contact with moisture, oxygen, and other corrosive elements in the environment.
Sacrificial protection: Zinc is a more reactive metal than steel or iron, so it acts as a sacrificial anode. If the zinc plating is damaged or scratched, the zinc will corrode preferentially before the substrate, sacrificing itself to protect the underlying metal.
Enhanced aesthetics: Zinc plating can provide a bright, shiny, and visually appealing finish to the metal surface. It can be further enhanced through post-plating processes such as chromate conversion coating or passivation.
Ductility and conductivity: Zinc plating does not significantly affect the mechanical or electrical properties of the substrate. It retains the base metal's ductility and conductivity, making it suitable for applications where these properties are important.
Zinc plating finds extensive use in industries such as automotive, construction, electronics, and manufacturing.
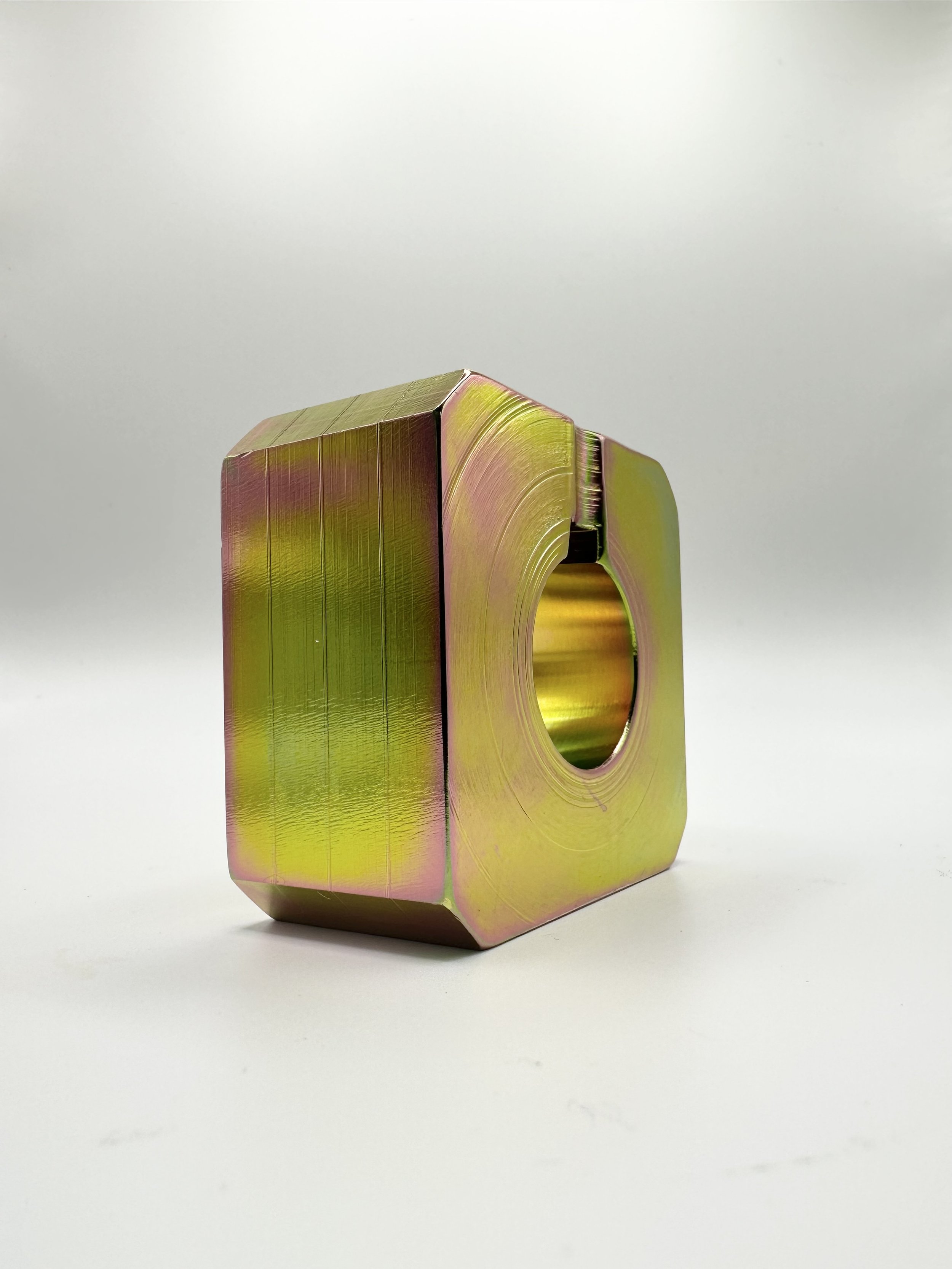
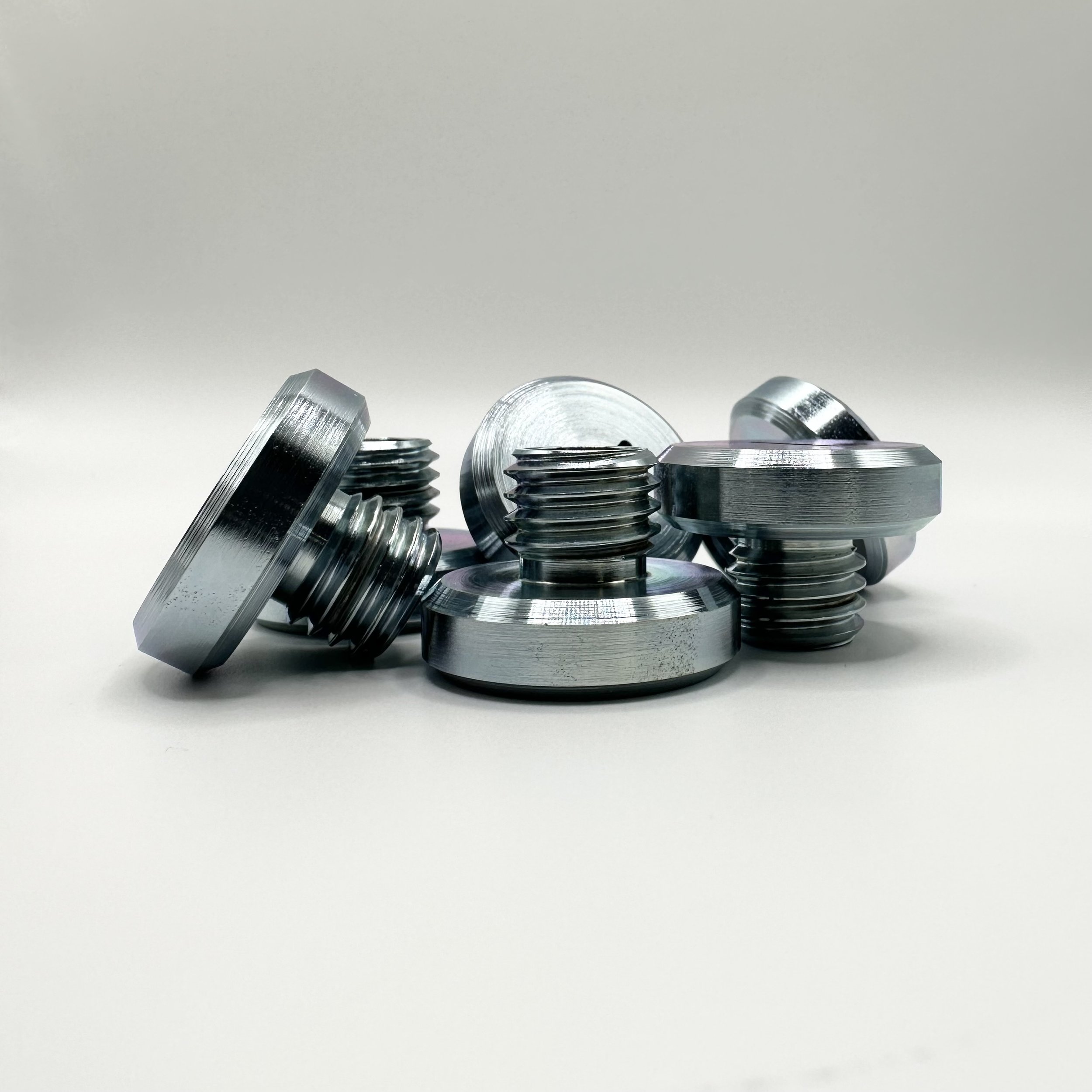
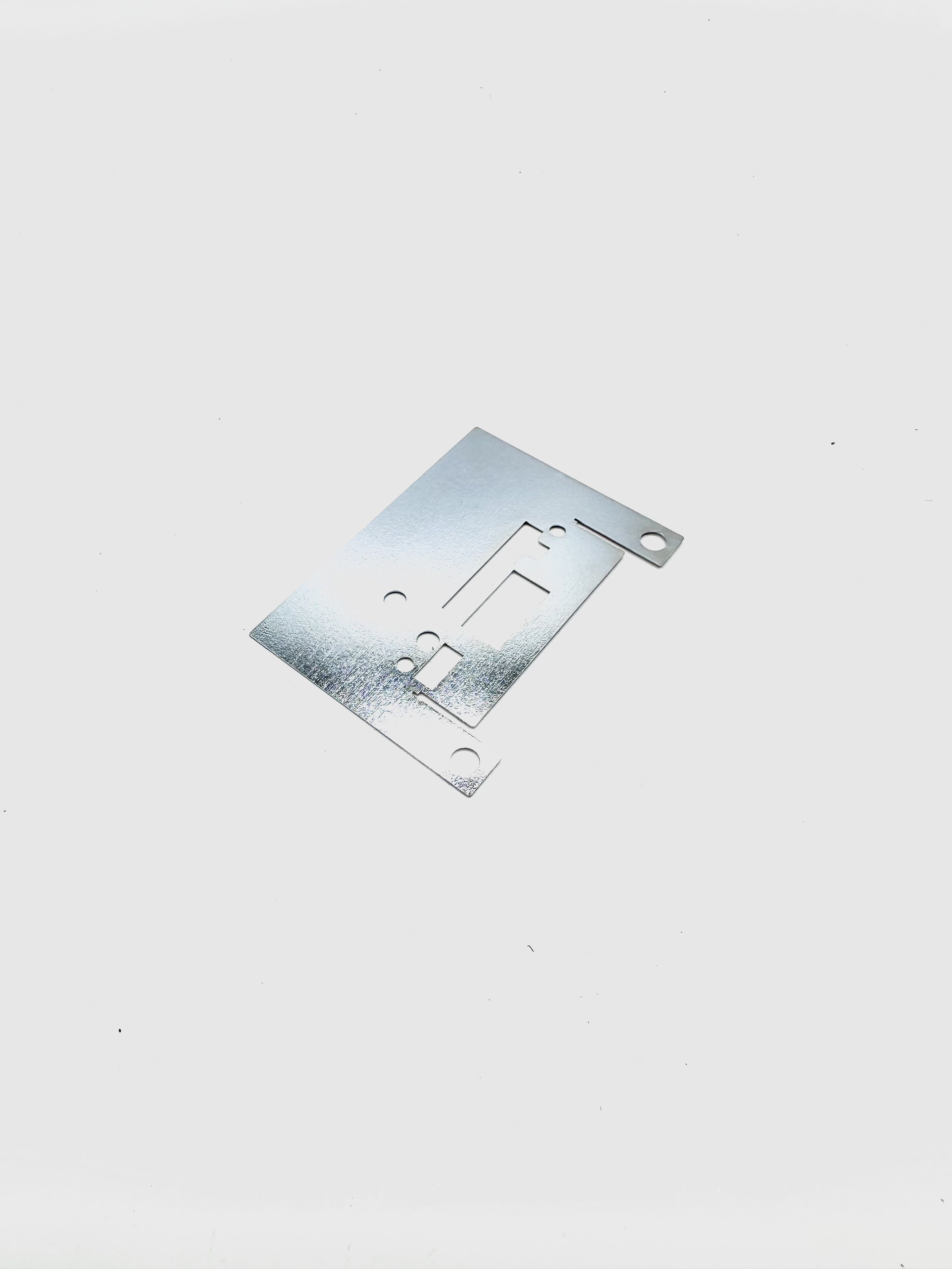
